5 Steps to a Successful Construction Safety Program
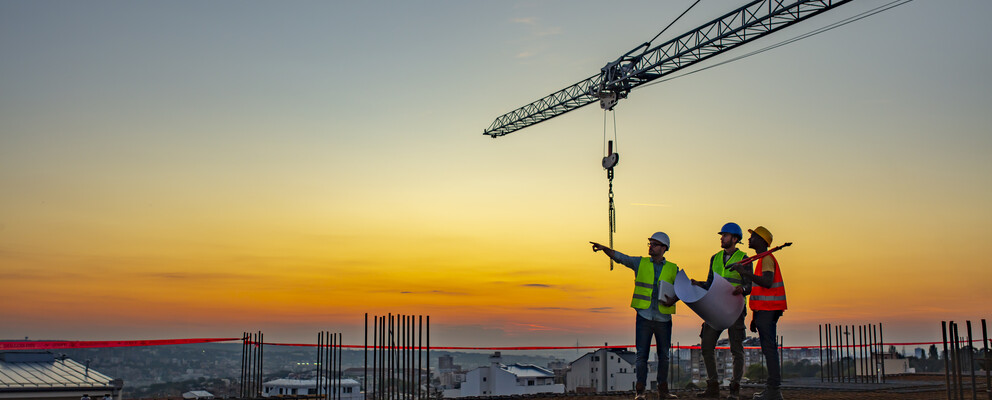
Construction workers account for a relatively small percentage of the total workforce – but they get seriously injured or killed on the job more often than workers in other industries.
The Occupational Safety and Health Administration (OSHA) recommends a proactive “find-and-fix” approach to construction hazards thatcenters around hazard identification, prevention and control.
In addition to enhancing workplace safety and reducing injuries, implementing a workplace health and safety program can bring about:
- Improvements in production and quality
- Better employee morale
- Improved employee recruiting and retention
- A more favorable image and reputation (among customers, suppliers, and the community)
Here are 5 bedrock principles of any construction safety program, along with practical action steps for implementation, adapted from OSHA guidance.
1. Management Leadership
Management leadership means that business owners, managers and supervisors make worker safety and health a core organizational value; commit to eliminating hazards, protecting workers and continuously improving safety and health on job sites; provide the necessary resources to implement and maintain the safety and health program; demonstrate and communicate their safety and health commitment to workers and others; and set an example through their own actions.
Communicate your commitment to a health and safety program
- Establish a written policy signed by top management describing the organization’s commitment to safety and health, and pledging to establish and maintain a safety program for all workers.
- Communicate the policy to all workers and, at appropriate times and places, to relevant parties, including:
- Contractors
- Subcontractors
- Staffing agencies
- Temporary workers at your worksite(s)
- Suppliers and vendors
- Other businesses in a multi-tenant building
- Visitors
- Customers
- Reinforce management commitment by considering safety and health in all business decisions, including:
- Estimating and bidding on projects
- Subcontractor and vendor selection
- Scheduling
- Implementing safety designs into construction processes, drawings and modifications
- Be visible in operations and set an example by following the same safety and health procedures you expect workers to follow.
- Conduct weekly or daily toolbox talks on safety and health and discuss/review safety and health indicators and/or open safety items on a “to do” list.
Define program goals
- Establish realistic, measurable goals for improving safety and health.
- Develop plans to achieve the goals by assigning tasks and responsibilities to particular people, setting timeframes and determining resource needs.
Allocate resources
- Estimate the resources needed to establish and implement the program. One example is ensuring safety equipment is included in the project budget.
- Allow time in workers’ schedules for them to fully participate in the program. Safety can be built into the labor rates when estimating a project.
- Integrate safety and health into planning and budgeting processes, and align budgets with program needs.
- Provide and direct resources to operate and maintain the program, meet safety and health commitments and pursue program goals.
Expect performance
- Identify a frontline person or people who will lead the safety program effort, make plans, coordinate activities and track progress.
- Define and regularly communicate responsibilities and authorities for implementing and maintaining the program.
- Hold people accountable for performance.
- Provide positive recognition for meeting or exceeding safety and health goals aimed at preventing injury and illness (e.g., reporting close calls/near misses, attending training, conducting inspections).
- Establish ways for management and all workers to communicate freely and often about safety and health issues, without fear of retaliation.
2. Worker Participation
There’s no way around it: In order to be effective, a safety and health program needs the meaningful participation of workers and their representatives. All workers should:
- Participate in the program and feel comfortable providing input and reporting safety or health concerns
- Have access to information they need to participate effectively in the program
- Have opportunities to participate in all phases of program design and implementation
- Be able to freely raise safety and health concerns; report injuries, illnesses and hazards; participate in the program; and exercise safety and health rights without fear of retaliation
Encourage workers to participate in the program
- Give workers the necessary time and resources to participate in the program.
- Acknowledge and provide positive reinforcement to those who participate in the program.
- Maintain an open-door policy that invites workers to talk to managers about safety and health and to make suggestions.
Encourage workers to report safety and health concerns
- Establish a simple process for workers to report injuries, illnesses, close calls/near misses, hazards and other safety and health concerns.
- Respond to reports promptly.
- Include an option for anonymous reporting to reduce fear of reprisal.
- Report back to workers routinely and frequently about action taken in response to their concerns and suggestions.
- Emphasize that management will use reported information only to improve job site safety and health, and that no worker will experience retaliation for bringing such information to management’s attention.
- Empower all workers to initiate or request a temporary suspension or shutdown of any work activity or operation they believe to be unsafe.
- Involve workers in finding solutions to reported issues.
Give workers access to safety and health information
- Give workers the information they need to understand safety and health hazards and control measures on the job site.
- Provide information to workers as required by OSHA, including:
- Safety Data Sheets (SDSs)
- Injury and illness data (prevent disclosure of sensitive and personal information as required)
- Results of worker exposure monitoring conducted at job sites (prevent disclosure of sensitive and personal information as required)
- Allow workers to review other useful information relating to health and safety, such as:
- Chemical and equipment manufacturer safety recommendations
- Job site equipment and vehicle inspection reports
- Incident investigation reports (prevent disclosure of sensitive and personal information as required)
- Job hazard analyses (JHAs) and/or job safety analyses (JSAs)
Involve workers in all aspects of the program
- Provide opportunities for workers to participate in all aspects of the program, including, but not limited to:
- Developing the program and setting goals to reduce or eliminate injuries and illnesses
- Reporting hazards and developing solutions that improve safety and health
- Analyzing hazards in each step of routine and nonroutine jobs, tasks and processes
- Defining and documenting safe work practices
- Conducting site inspections, including equipment and vehicles
- Developing and revising safety procedures
- Participating in incident and close call/near miss investigations
- Training current coworkers and new hires
- Developing, implementing, and evaluating training programs
- Evaluating program performance and identifying ways to improve it
- Taking part in exposure monitoring and medical surveillance associated with health hazards
- Conduct daily planning meetings, huddles, toolbox talks or tailgate meetings to engage workers in the safety and health program.
Remove barriers to participation
- Ensure that workers from all levels of the organization can participate regardless of their skill level, education or language.
- Provide frequent and regular feedback to show employees that their safety and health concerns are being heard and addressed.
- Authorize sufficient time and resources to facilitate worker participation; for example, hold safety and health meetings during regular working hours.
- Ensure that the program protects workers from being retaliated against for reporting injuries, illnesses and hazards; participating in the program; or exercising their safety and health rights. Ensure that other policies and programs do not discourage worker participation.
- Post the Section 11(c) Fact Sheet in the workplace or otherwise make it available for easy access by employees.
- Design incentive programs (such as point systems, awards and prizes) in a way that does not discourage the reporting of injuries, illnesses and near misses.
3. Hazard Identification and Assessment
In construction, unanticipated hazards can arise due to changes in project timelines, sequence of events and the fast pace of projects. Hazard identification and assessment is a crucial part of an effective safety and health program.
Collect existing information about job site hazards
- Collect, organize and review information with workers to determine what types of hazards may be present and which workers may be exposed or potentially exposed, including:
- Equipment and machinery operating manuals
- SDSs provided by chemical manufacturers
- Self-inspection reports and inspection reports from insurance carriers, government agencies and consultants
- Records of previous injuries and illnesses, such as OSHA 300 and 301 logs and reports of incident investigations
- Workers’ compensation records and reports
- Patterns of frequently occurring injuries and illnesses
- Exposure monitoring results, industrial hygiene assessments, and medical records (appropriately redacted to ensure patient/worker privacy)
- Existing safety and health programs (hazard communication, confined spaces in construction, respiratory protection, process safety management, PPE, etc.)
- Input from workers, including surveys or minutes from safety and health committee meetings
- Results of job hazard analyses (also known as job safety analyses)
- Provide relevant information from reputable outside sources, including:
- OSHA, National Institute for Occupational Safety and Health (NIOSH) and Centers for Disease Control and Prevention (CDC) websites, publications and alerts
- Trade associations
- Labor unions, state and local occupational safety and health committees/coalitions (“COSH groups”) and worker advocacy groups
- Safety and health consultants
Inspect the job site for safety hazards
- Designate a competent person to conduct frequent and regular inspections of the job sites, materials and equipment.
- Include workers on the inspection team, and talk to them about hazards that they see or report.
- Plan ahead to anticipate the potential introduction of additional hazards by the next group of trades or sequence of construction activities and to address these additional hazards. For example, ensure that structures can handle any additional anticipated loads
- Document inspections so you can later verify that hazardous conditions have been corrected. Take photos or video of problem areas to facilitate on-the-job discussion and brainstorming about how to immediately control them.
- Include all areas and activities in these inspections, including:
- Trenching and excavations
- Staging areas
- Layout yards
- Working at heights
- Materials storage
- Heavy equipment maintenance
- Activities of on-site contractors, subcontractors and temporary workers
- Regularly inspect both mobile construction equipment (e.g., forklifts, bulldozers, aerial lifts and cranes) and transportation vehicles (e.g., cars, trucks).
- Create material delivery areas and internal traffic control plans for the construction site and laydown areas.
- Use checklists that highlight things to look for. Typical hazards fall into several major categories, such as:
- Slip, trip, and fall hazards
- Electrical hazards
- General housekeeping
- Equipment operation
- Equipment maintenance
- Fire protection
- Work organization and process flow (including staffing and scheduling)
- Work practices
- Ergonomic problems
- Lack of emergency procedures
- Seek the input of workers and evaluate potential hazards and related risks before:
- Changing operations, workstations or workflow
- Making major organizational changes
- Introducing new equipment, materials or processes
Identify health hazards
- Identify chemical hazards—review SDSs and product labels to identify chemicals at your job site that have low exposure limits, are highly volatile or are used in large quantities or in unventilated spaces.
- Identify activities that may result in skin exposure to chemicals.
- Identify physical hazards, including:
- Excessive noise (areas where you must raise your voice to be heard by others)
- Elevated heat (indoor and outdoor)
- Sources of radiation (radioactive materials, X-rays, or radiofrequency radiation)
- Identify biological hazards, including:
- Sources of infectious diseases
- Molds and toxic or poisonous plants
- Animal materials (fur or scat) capable of causing allergic reactions or occupational asthma
- Identify ergonomic risk factors—examine work activities that require heavy lifting, work above shoulder height, repetitive motions or tasks with significant vibration.
- Conduct quantitative exposure assessments when possible, using air sampling or direct reading instruments.
- Review OSHA 300 logs to help identify health hazards associated with job site exposures.
Conduct incident investigations
- Develop a clear plan and procedure for conducting incident investigations, so that an investigation can begin immediately when an incident occurs. The plan should cover items such as:
- Who will be involved
- Lines of communication
- Materials, equipment and supplies needed
- Reporting forms and templates
- Train investigative teams on incident investigation techniques, emphasizing objectivity and open-mindedness throughout the investigation process.
- Conduct investigations with a trained team that includes both worker and management representatives.
- Investigate close calls and near misses.
- Identify and analyze root causes to address underlying program shortcomings that allowed the incidents to happen.
- Communicate the results of the investigation to managers, supervisors and workers to prevent recurrence
Identify hazards associated with emergency and nonroutine situations
- Identify foreseeable emergency scenarios and nonroutine tasks, taking into account the types of material and equipment in use and the location at the worksite.
- Scenarios such as the following may be foreseeable:
- Structural collapse (e.g., bridges, buildings, trenches and concrete forms)
- Nonroutine tasks, such as infrequently performed activities (e.g., critical lifts and concrete pours)
- Fires and explosions
- Medical emergencies
- Weather emergencies and natural disasters
- Hazardous material spills
- Startups after planned or unplanned equipment shutdowns
Characterize the nature of identified hazards, identify interim control measures, and prioritize the hazards for control
- Evaluate each hazard by considering the severity of potential outcomes, the likelihood that an event or exposure will occur and the number of workers who might be exposed.
- Use interim control measures to protect workers until more permanent solutions can be implemented.
- Prioritize the hazards so that those presenting the greatest risk are addressed first. (Note, however, that employers have an ongoing obligation to control all serious recognized hazards and to protect workers.)
4. Hazard Prevention and Control
Effective controls protect workers from hazards; help avoid injuries, illnesses and incidents; minimize or eliminate safety and health risks; and help employers provide workers with safe and healthful working conditions.
Identify control options
- Review sources such as OSHA standards and guidance, industry consensus standards, NIOSH publications, manufacturers’ literature and engineering reports to identify potential control measures.
- Keep current on relevant information from trade or professional associations.
- Investigate control measures used at other worksites and determine whether they would be effective at your job sites.
- Get input from workers who may be able to suggest and evaluate solutions based on their knowledge of the job site, equipment and work processes.
- For complex hazards, consult with safety and health experts, including OSHA’s On-Site Consultation Program.
- Plan the sequencing of various trades to reduce overlap where possible and to avoid exposing other trades to hazards.
Select controls
- Immediately eliminate or control all serious hazards (hazards that are causing or are likely to cause death or serious physical harm).
- Use interim controls while you develop and implement longer-term solutions.
- Select controls according to a hierarchy that emphasizes engineering solutions (including elimination or substitution) first, followed by safe work practices, administrative controls and finally PPE.
- Avoid selecting controls that may directly or indirectly introduce new hazards. Examples include exhausting contaminated air into occupied work spaces or using hearing protection that makes it difficult to hear backup alarms.
- Review and discuss control options with workers to ensure that controls are feasible and effective.
- Use a combination of control options when no single method fully protects workers.
Develop and update a hazard control plan
- List the hazards needing controls in order of priority.
- Assign responsibility for installing/implementing the controls to a specific person or people with the power or ability to implement the controls.
- Establish a target completion date.
- Plan how you will track progress toward completion.
- Plan how you will verify the effectiveness of controls after they are installed or implemented.
Select controls to protect workers during nonroutine tasks and emergencies
- Develop procedures to control hazards that may arise during nonroutine tasks (e.g., mobilization and demobilization of the site, critical lifts with cranes, concrete pours or setting critical structural members).
- Develop or modify plans to control hazards that may arise in emergency situations.
- Procure any equipment needed to control emergency-related hazards.
- Assign responsibilities for implementing the emergency plan.
- Conduct emergency drills to ensure that procedures and equipment provide adequate protection during emergency situations.
Implement selected controls on the job site
- Implement hazard control measures according to the priorities established in the hazard control plan.
- When resources are limited, implement measures on a “worst-first” basis, according to the hazard ranking priorities (risk) established during hazard identification and assessment. (Note, however, that regardless of limited resources, employers have an obligation to protect workers from recognized, serious hazards.)
- Promptly implement any measures that are easy and inexpensive—such as general housekeeping, removal of obvious tripping hazards such as electrical cords and basic lighting—regardless of the level of hazard they involve.
Follow up to confirm that controls are effective
- Track progress and verify implementation by asking the following questions:
- Have all control measures been implemented according to the hazard control plan?
- Have engineering controls been properly installed and tested?
- Have workers been appropriately trained so that they understand the controls, including how to operate engineering controls, safe work practices and PPE use requirements?
- Are controls being used correctly and consistently?
- Conduct regular inspections (and industrial hygiene monitoring, if indicated) to confirm that engineering controls are operating as designed.
- Evaluate control measures to determine if they are effective or need to be modified. Involve workers in the evaluation of the controls.
- If controls are not effective, identify, select and implement further control measures that will provide adequate protection.
- Confirm that work practices, administrative controls and PPE use policies are being followed.
- Conduct routine preventive maintenance of equipment and controls to help prevent incidents due to equipment failure.
5. Education & Training
Education and training are important tools for informing workers and managers about hazards and controls so they can work more safely and be more productive. Another role of education and training, however, is to provide workers and managers with a greater understanding of the safety and health program itself, so they can contribute to its development and implementation.
Provide program awareness training
- Provide training to all managers; supervisors; workers; and contractor, subcontractor and temporary agency workers on:
- Safety and health policies, goals and procedures
- Functions of the safety and health program
- Whom to contact with questions or concerns about the program (including contact information)
- How to report hazards, injuries, illnesses and close calls/near misses
- What to do in an emergency
- The employer’s responsibilities under the program
- Workers’ rights under the OSH Act
- Provide information on the safety and health hazards of the job site and the controls for those hazards.
- Ensure that training is provided in the language(s) and at a literacy level that all workers can understand.
- Emphasize that the program can only work when everyone is involved and feels comfortable discussing concerns; making suggestions; and reporting injuries, incidents and hazards.
- Confirm, as part of the training, that all workers have the right to report injuries, incidents, hazards and concerns and to fully participate in the program without fear of retaliation.
Train employers, managers, and supervisors on their roles in the program
- Reinforce employer, manager and supervisor knowledge of their responsibilities under the OSH Act and workers’ rights guaranteed by the Act.
- Train employers, managers and supervisors on procedures for responding to workers’ reports of injuries, illnesses and incidents, including ways to avoid discouraging reporting.
- Instruct employers, managers and supervisors on fundamental concepts and techniques for recognizing hazards and methods of controlling them.
- Instruct employers, managers and supervisors on incident investigation techniques, including root cause analysis.
- As a starting point, consider providing the OSHA 30-hour construction safety course, or a similar course
Train workers on their specific roles in the safety and health program
- Instruct workers on how to report injuries, illnesses, incidents and concerns.
- If a computerized reporting system is used, ensure that all employees have the basic computer skills and computer access sufficient to submit an effective report.
- Instruct workers assigned specific roles within the safety and health program on how they should carry out those responsibilities, including:
- Hazard recognition and controls
- Participation in incident investigations
- Program evaluation and improvement
- Provide opportunities for workers to ask questions and provide feedback during and after the training.
- As the program evolves, institute a more formal process for determining the training needs of workers responsible for developing, implementing and maintaining the program.
Train workers on hazard identification and controls
- Train workers on techniques for identifying hazards, such as job hazard analysis (see OSHA Publication 3071).
- Train workers so they understand and can recognize the hazards they may encounter in their own jobs, as well as more general work-related hazards.
- Instruct workers on concepts and techniques for controlling hazards, including the hierarchy of controls and its importance.
- Train workers on the proper use of work practice and administrative controls.
- Train workers on when and how to wear required PPE.
Provide additional training, as necessary, when construction progresses. Consider situations such as when new trades and/or equipment arrive at the job site to perform the next phase of the project.
Safety standards can’t be ignored
Training workers in safe work practices, and leading by example from the top down, are paramount.
Making safety information available to employees and encouraging them to follow the rules will result in a more productive worksite. When shortcuts are taken, there’s a price to pay, whether through death, injury, increased insurance costs, poor publicity following an accident or even having to redo the job.
Do you need assistance creating an effective risk management strategy for your construction business? Contact your insurance professional for insurance strategies and additional safety tips to protect your workers and your bottom line.